1. Introduction
In the era of Industry 4.0, factory maintenance has undergone a transformative shift, leveraging digital technologies to enhance efficiency, reliability, and sustainability. Digitalized environments in manufacturing are characterized by the integration of advanced technologies such as the Internet of Things (IoT), artificial intelligence (AI), big data analytics, and cloud computing. These technologies provide real-time insights into equipment performance, enabling predictive maintenance and reducing unplanned downtime. Predictive maintenance utilizes sensor data to forecast equipment failures, allowing preemptive action that minimizes disruptions and maintenance costs. This approach not only improves equipment longevity but also optimizes resource allocation by scheduling maintenance activities at the most opportune times.
Real-time monitoring through IoT devices ensures continuous visibility into machine health and operational status, facilitating immediate response to anomalies and maintaining optimal production levels. Automated maintenance scheduling systems further enhance efficiency by generating work orders and dispatching technicians based on predictive analytics, reducing planning time and improving schedule adherence. Digitalized environments also streamline spare parts management; AI-powered systems analyze usage patterns and predict future requirements, ensuring the timely availability of necessary parts while avoiding overstocking.
Sustainability is another critical benefit, as digital technologies help reduce energy consumption and waste through smart energy management systems, optimizing machine operations and minimizing idle times. Additionally, continuous improvement is driven by machine learning and data analytics, which identify inefficiencies and suggest optimizations, leading to substantial productivity gains.
2. Challenges faced by smart factories
Real-time visibility into machinery and asset status is crucial for efficient smart factory operations. Without it, equipment malfunctions or performance degradation can go unnoticed, leading to disruptions, increased downtime, and higher repair costs. This results in reactive maintenance, inefficient production, and difficulties in maintaining product quality. Poor resource management can cause bottlenecks, increased operational costs, and unanticipated equipment failures that disrupt workflow. Data-driven decision-making is essential for optimizing operations, identifying trends, and making informed decisions. Managing spare parts inventory requires balancing overstocking and understocking to avoid tying up capital and storage space or disrupting operations.
3. New technologies adopted to overcome challenges
By adopting advanced technologies, smart factories can overcome challenges related to equipment reliability, operational efficiency, and sustainability. By leveraging IoT, AI, big data analytics, and cloud computing, smart factories can achieve comprehensive real-time monitoring and predictive maintenance of their equipment, resources, and assets. This proactive approach allows for early detection of potential issues, minimizing unplanned downtime and extending equipment lifespan. Additionally, automated maintenance scheduling and intelligent spare parts management optimize resource allocation, leading to significant cost savings. These technologies also enhance sustainability efforts by reducing energy consumption and waste. Overall, the integration of these advanced technologies transforms factory maintenance, driving improved reliability, efficiency, and sustainability across industrial operations
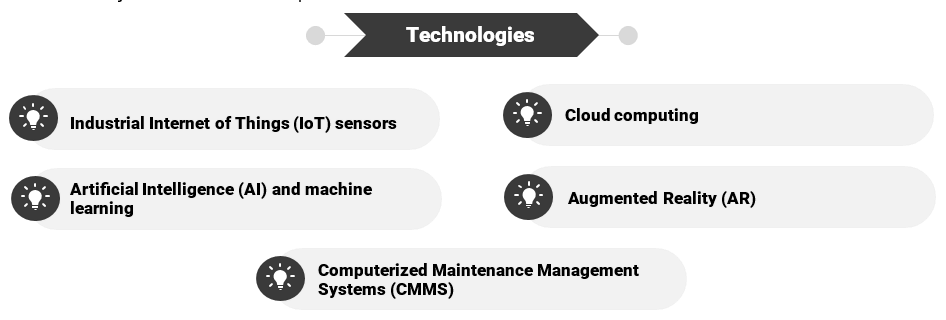
- IoT sensors for real-time equipment monitoring: IoT sensors provide continuous real-time data on equipment conditions, enabling early detection of anomalies and minimizing interruptions. Maintenance is optimized based on actual conditions, reducing unnecessary costs
- Cloud computing enabling remote and mobile maintenance: Cloud computing allows maintenance teams to access critical data and applications from any location, facilitating remote management and real-time collaboration. It supports seamless integration of systems, ensuring synchronized factory operations
- AI and machine learning for predictive maintenance: AI and machine learning analyze historical and real-time data to predict equipment failures, enabling timely interventions. They optimize maintenance schedules and enhance automation, increasing productivity and reducing human error
- AR for guided repairs and staff training: AR provides real-time guidance through visual overlays, helping technicians perform complex repairs accurately. It offers risk-free hands-on training, improving skill development and maintenance efficiency
- CMMS for centralized information and automated processes: CMMS centralizes maintenance information and automates tasks like scheduling and inventory management, reducing administrative workload. It streamlines maintenance operations, ensuring efficient resource use and well-organized processes
Examples of companies using technology to improve their maintenance operations
- Siemens uses AI to predict failures in their gas turbines by analyzing vibration data. This has reduced unplanned downtime and maintenance costs
- GE’s Predix platform utilizes AI and ML to predict failures in industrial equipment, leading to significant savings in maintenance costs and improved equipment uptime
- IBM’s Maximo uses AI to automate work order generation and dispatch the right technician for the job, improving efficiency and response times
- SAP Predictive Maintenance and Service integrates with field service management to automate technician dispatch, reducing downtime
- SKF’s Enlight Centre uses predictive analytics to manage spare parts inventory, reducing excess inventory and minimizing downtime
- DHL employs AI to forecast spare parts demand in their logistics operations, improving inventory accuracy and reducing costs
- Honeywell Forge offers remote monitoring and diagnostics for industrial equipment, enabling proactive maintenance and reducing the need for on-site visits
- Schneider Electric’s EcoStruxure allows remote monitoring of electrical distribution systems, identifying issues before they become critical
- Toyota uses ML to analyze production data and identify areas for improvement in their maintenance processes, leading to enhanced efficiency and reduced downtime
- Hitachi’s Lumada platform leverages ML to provide continuous insights and recommendations for optimizing maintenance operations
4. Benefits of CMMS implementation
The implementation of CMMS plays a pivotal role in enhancing maintenance practices by providing real-time visibility, optimizing resources, enabling preventive planning, and leveraging data analytics. These tools streamline work order management, asset tracking, and inventory management, reducing costs and improving efficiency. Customizable workflows and user-friendly interfaces ensure ease of use, while detailed reporting and KPI tracking enable continuous improvement in maintenance operations.
Major benefits of CMMS:
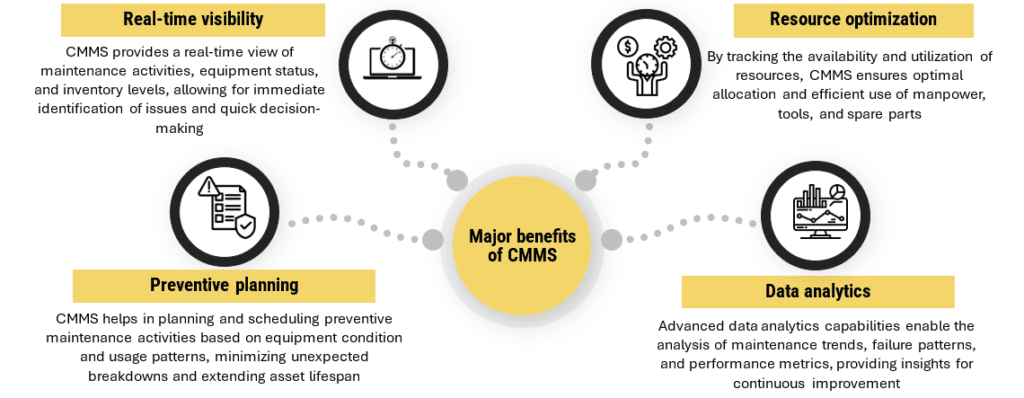
Other benefits of CMMS:
- Work order management: CMMS automates work order creation, assignment, and tracking, ensuring timely completion and maintaining detailed asset records for proactive maintenance
- Inventory management: CMMS tracks inventory levels, provides low stock alerts, and optimizes procurement processes, reducing carrying costs and waste
- Workflow customization and user access: CMMS customizes workflows to enhance efficiency, offers user-friendly interfaces, and provides mobile access for on-the-go updates
- Reporting and performance metrics: CMMS generates reports and tracks KPIs like MTTR and MTBF, helping identify areas for improvement and track the effectiveness of corrective actions
4.1. Case studies on the implementation of technologies and their impact
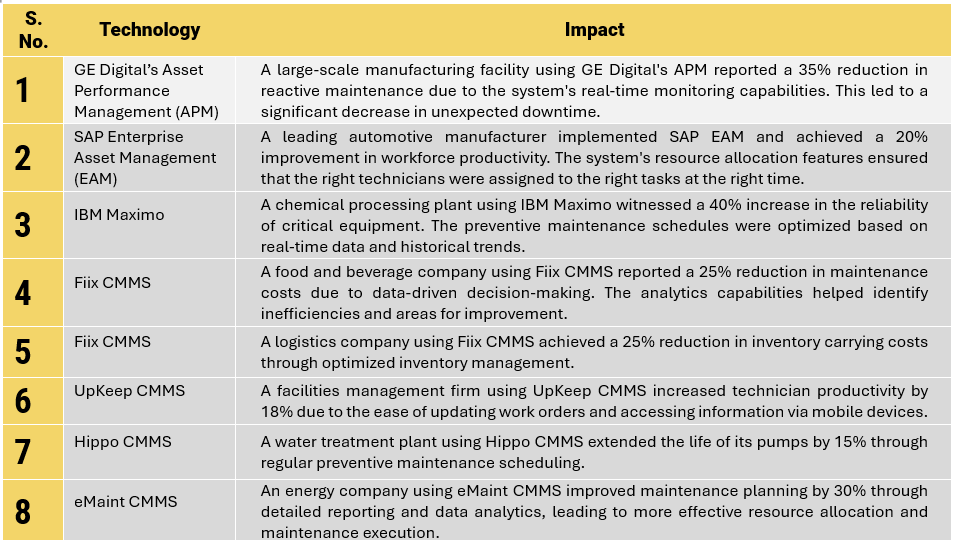
5. Meeting sustainability goals through maintenance practices
Achieving sustainability commitments in smart factories is significantly enhanced through advanced maintenance practices. Smart factories can improve their sustainability performance by extending equipment life, reducing unplanned downtime, optimizing resource utilization, maintaining equipment efficiency, and ensuring regulatory compliance. These practices lead to cost savings and operational efficiencies and contribute to a reduced environmental impact, aligning with broader sustainability goals.
Using data analytics, proactive maintenance, sustainable optimization, and proper adherence to schedules, smart factories can reduce waste, emissions, and downtime while extending lifespan, meeting regulations, and ensuring safe operations. Predictive and preventive techniques identify issues before failures, minimizing emergency repairs and premature replacements. Efficient inventory management, preventive scheduling, and energy-efficient equipment optimize the use of materials, energy, and resources. Proper maintenance keeps equipment operating at peak efficiency, leading to energy savings and reduced emissions by addressing issues like misalignment, imbalance, or fouling with vibration analysis and thermal imaging. By implementing these strategies, factories can lower their environmental impact, reduce costs, and maintain a safe and compliant operation.
5.1. Case studies on meeting sustainability goals
Case studies: Meeting sustainability goals through maintenance techniques and practices
Overview: Siemens Energy uses advanced predictive maintenance techniques to extend the life of its turbines. Impact: Predictive maintenance strategies based on real-time data analysis and machine learning algorithms enable early detection of wear and tear, allowing timely interventions. Siemens Energy reported that the implementation of predictive maintenance led to a 30% increase in the lifespan of critical turbine components. |
Overview: Nestlé implemented a CMMS to reduce unplanned downtime in its manufacturing plants. Impact: By using CMMS, Nestlé was able to schedule maintenance activities more effectively and predict potential failures before they occurred. This led to fewer production interruptions and lower maintenance costs, contributing to more sustainable operations. Nestlé reported a 40% reduction in unplanned downtime and associated costs. |
Overview: Toyota employs lean manufacturing principles supported by advanced maintenance systems to optimize resource utilization. Impact: CMMS and IoT sensors provide real-time data on resource usage, enabling precise monitoring and management. This data-driven approach helps identify inefficiencies and optimize the use of materials, energy, and labor, reducing waste and environmental impact. Toyota achieved a 25% reduction in waste and improved overall resource efficiency. |
Overview: GE uses a combination of IoT and predictive analytics to maintain equipment efficiency and achieve energy savings. Impact: Continuous monitoring of equipment performance ensures that machines operate at optimal efficiency. Predictive maintenance allows for timely interventions to prevent performance degradation, leading to significant energy savings and reduced carbon footprint. GE reported a 15% reduction in energy consumption across its facilities. |
Overview: Dow Chemical uses CMMS to ensure compliance with regulatory and safety standards. Impact: CMMS systems track and document all maintenance activities, ensuring that they meet regulatory requirements and safety standards. Regular maintenance and inspections prevent hazardous conditions, protecting both workers and the environment. Dow Chemical achieved a 20% reduction in compliance-related incidents. |
Overall, the digitalization of factory maintenance transforms traditional reactive approaches into proactive, efficient, and sustainable practices, promising significant cost savings, reduced downtime, and enhanced operational performance. As these technologies evolve, the potential for further advancements in factory maintenance continues to expand, offering even greater benefits for the manufacturing industry.