Engagement Overview:
An organic food manufacturing company with facilities in more than 15 countries across the globe wanted to transform its supply chain and third-party logistics (3PL) operations in the Chinese region. They sought Infiniti’s help to identify supply chain risks and develop strategies to mitigate them. By collaborating with Infiniti Research, the client was able to reduce their annual spend for supply chain management and transportation by 23%.
Organic food manufacturing market Overview
Over the past decade, the organic food manufacturing market has been performing well despite the economic downturn. However, increasing globalization, regulations, and competition are rising challenges for companies operating in the organic food manufacturing market. Besides, supply chain complexities and operational risks are increasing challenges for organic food manufacturing companies. As such, it is becoming imperative for companies in the organic food manufacturing market to identify supply chain risks, develop mitigation plans, and build resilient and agile supply chains for the future. This is where Infiniti’s risk assessment solution comes into play. By leveraging Infiniti’s risk assessment solution, food manufacturing companies can reduce supply vulnerability and ensure business continuity.
As the supply chain operations are severely impacted owing to the COVID-19 crisis, companies in the organic food manufacturing market must build resilient and agile supply chains to effectively mitigate supply chain risks and ensure business continuity. RFP to learn how our COVID-19 business continuity support solutions can help food manufacturing firms achieve this strategic objective.
Business Challenges Faced:
Our client, a Chinese organic food manufacturing company, faced challenges in managing supply risks arising from various factors such as single supplier sourcing, supplier capacity constraints, and supply quality issues. Also, as the client partnered with multiple third-party logistics (3PL) providers and co-packing suppliers to manage its supply chain processes, they faced difficulties in coordinating with them and ensuring timely delivery. The organic food manufacturing market client, therefore, wanted to build resilient and agile supply chains to effectively mitigate supply chain risks. Besides, they wanted to drive higher-cost efficiencies through strategic sourcing and warehouse management. They chose to partner with Infiniti Research to leverage their expertise in offering risk assessment solution.
By leveraging Infiniti’s risk assessment solution, the client also wanted to:
- Identify all threats to supply continuity
- Establish a detailed supply risk assessment mechanism to identify supply risks and proactively work toward mitigating them
- Optimize warehouse management and operations, inbound and outbound transportation, and co-packing processes
Our Integrated Approach:
As a part of the risk assessment solution, the experts at Infiniti Research worked closely with the client’s in-house team to examine the company’s supply chain complexities. This phase of the engagement also involved a detailed evaluation of various supply risk parameters to develop a holistic supply risk assessment model.
In the second phase, our experts developed a strategic sourcing road map for the client and also conducted extensive market research to identify a list of potential suppliers with the capabilities and infrastructure necessary to fulfil the client’s requirements.
In the next phase, the supply risk assessment model was customized based on the client’s process parameters. This model factored nine unique parameters to quantify the risk and helped the Organic food manufacturing market client prioritize areas that required immediate risk mitigation plans.
To ensure effective mitigation of risks, organic food manufacturing companies must have a structured risk management strategy in place with the primary objective of reducing supply vulnerability and ensuring business continuity. Contact us to learn more about our risk assessment and management solutions.
Business Outcome:
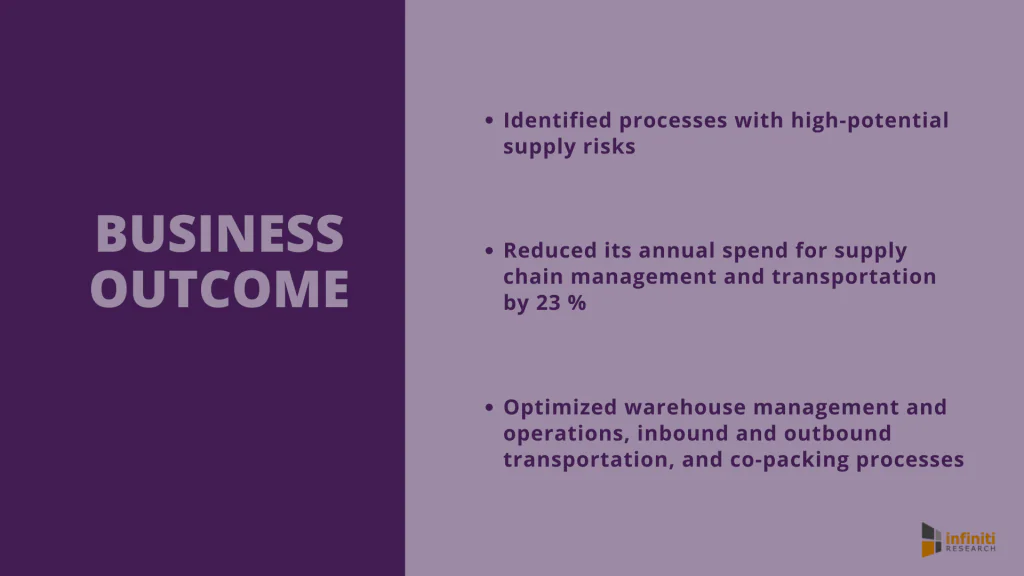
The experts at Infiniti Research helped the client to identify processes with high-potential supply risks and provided a mechanism for category managers to collaborate with cross-functional teams like R&D to work on risk mitigation plans. Also, the risk assessment model developed by Infiniti helped the client to identify processes with high supply risks and prioritize development of risk mitigation strategies. This helped the client to reduce the risk on its operations through measures such as supplier quality assurance, alternative supplier development, and sourcing from alternative regions.
The organic food manufacturing market client also benefited from improved visibility of cost breakdown as it gained the ability to identify inefficient processes and opportunity areas. Besides, the visibility and control helped the client to understand the impact of factors like volume variations, budgeting, and price drivers’ variation. The client was also able to reduce its number of suppliers to two. Besides, the inbound transport services were eliminated by consolidating operations to one site and this led to lead-time reduction of more than 10%. With Infiniti’s risk assessment solution, the Organic food manufacturing market client was also able to reduce its annual spend for supply chain management and transportation by 23 %.
Want to learn more about our COVID-19 business continuity support solutions and their benefits for your business? Request more info here.