Introduction
In recent years, automation has transformed the manufacturing industry, enabling companies to increase productivity, enhance efficiency, and maintain consistent quality. The integration of advanced technologies, including robotics and artificial intelligence (AI), has shifted manufacturing from traditional manual processes to a system driven by high-tech automation solutions. This article will explore the importance of automation in the manufacturing industry, discuss its various applications, and analyze its impact and future role in shaping the industry.
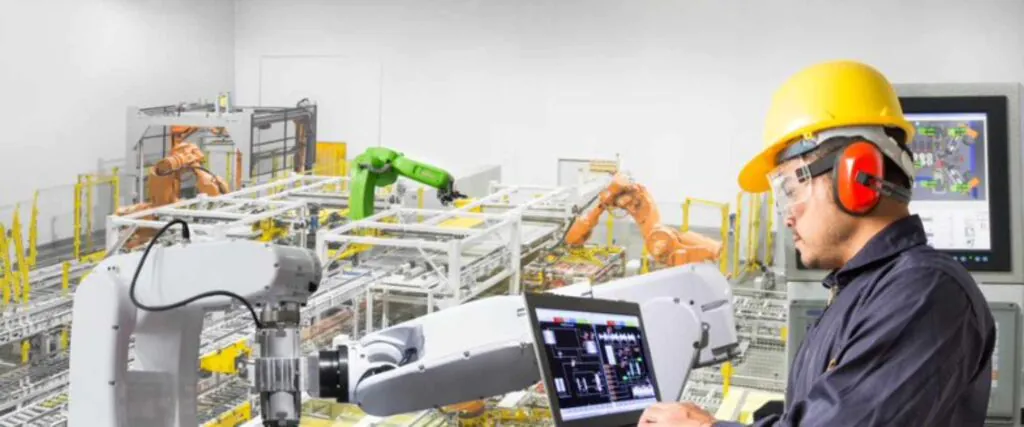
Importance of Automation in the Manufacturing Industry
Automation’s role in manufacturing is crucial as it addresses multiple challenges, including labor shortages, rising production costs, and the demand for enhanced product quality. Some key benefits include:
Importance of Automation in the Manufacturing Industry
Increased Productivity
Consistent Quality
Cost Savings
Enhanced Worker Safety
Increased Productivity
Automated machines can operate 24/7, allowing for continuous production cycles that human labor cannot match. This heightened productivity is essential for companies aiming to meet growing consumer demands.
Consistent Quality
Automation helps maintain uniformity and minimizes errors by following precise instructions. This consistency improves the quality of goods and reduces waste, which is essential in industries requiring high accuracy, such as electronics and pharmaceuticals.
Cost Savings
While automation can require a high initial investment, the reduction in labor costs and wastage, along with higher productivity, allows businesses to recoup costs and save money over the long term.
Enhanced Worker Safety
Automation can handle hazardous tasks, minimizing the risk of injury to human workers. This creates a safer working environment and can lead to improved job satisfaction and morale.
These advantages illustrate why the importance of automation in the manufacturing industry has grown, with more companies seeing it as a strategic investment to maintain competitiveness.
Types of Automation in Manufacturing
Automation in manufacturing isn’t one-size-fits-all. There are various types of automation systems that manufacturers can use based on their specific needs:
a) Fixed Automation
Also known as hard automation, fixed automation involves using machinery for a specific, repeated task. This is ideal for high-volume production as the machinery is designed to execute one function repetitively without the need for reconfiguration. Examples include car assembly lines and packaging processes.
b) Programmable Automation
This type of automation allows reprogramming machinery to accommodate different tasks, making it suitable for batch production. While not as flexible as robotic systems, it is more adaptable than fixed automation. Companies producing different versions of a product or manufacturing in smaller batches often opt for programmable automation.
c) Flexible Automation
Flexible automation provides even more adaptability than programmable automation. Robots, for instance, can handle various tasks with minimal downtime between changeovers, making it possible to switch from one product to another quickly. Flexible automation is essential in industries where customization is important.
d) Robotic Process Automation (RPA)
Robotic Process Automation (RPA) in manufacturing is distinct from traditional automation; it is software-based and primarily used for repetitive administrative tasks like order processing, inventory management, and data entry. RPA software can interface with different digital systems to streamline workflows, saving companies time and reducing human error.
Each type of automation offers unique benefits depending on the scale, type, and objectives of a manufacturing operation. The right choice enhances efficiency and addresses specific production needs.
Use of Automation in Manufacturing Industry
The use of automation in the manufacturing industry has expanded across several applications, from handling physical production tasks to managing data-related processes. Below are some common uses of automation in manufacturing:
a) Assembly Line Automation
Automated assembly lines utilize machinery and robots to assemble components with high accuracy and speed. This process is particularly prevalent in automotive and electronics manufacturing, where consistent precision is critical. Automation in assembly lines allows companies to produce more units without compromising quality.
b) Quality Control and Inspection
Automated inspection systems using computer vision, sensors, and AI can detect defects at every stage of production. Real-time monitoring ensures only quality products proceed to the next stage, reducing wastage and enhancing reliability. AI-driven inspection can identify microscopic defects that human inspectors might overlook.
c) Material Handling and Inventory Management
Automated systems handle heavy and dangerous materials safely. Technologies like autonomous guided vehicles (AGVs) and robotic arms are commonly used to transport raw materials, manage inventories, and streamline logistics in warehouses and production floors.
d) Packaging and Shipping
Automation in packaging and shipping increases accuracy and speeds up the final stage of production. Robots equipped with barcode scanners and sensors can accurately pack products, label them, and prepare them for shipping, thereby minimizing manual labor and reducing errors.
e) Data Management and Administrative Tasks
Robotic Process Automation (RPA) can streamline administrative tasks, such as managing inventory records, processing purchase orders, and tracking shipments. By automating these processes, companies can maintain accurate records and reduce operational overheads.
Automation’s versatility across various manufacturing processes helps companies become more agile, meet regulatory standards, and achieve greater efficiency.
Role of Robotics in Automation
Robotics plays a central role in automation, offering new possibilities for high precision and adaptability. Robotic applications in manufacturing include:
Welding and Soldering
Robotic arms perform precision welding in industries like automotive and aerospace, where complex structures require accurate assembly.
Machine Loading and Unloading
Robots load raw materials into machines and unload finished parts. This task minimizes labor demand and accelerates the production cycle.
Inspection and Testing
Robots equipped with vision systems inspect products at multiple stages, ensuring they meet specifications and reduce faulty products reaching customers.
In addition to these, collaborative robots, or cobots, are increasingly popular. Cobots work alongside human operators, enhancing productivity while allowing the flexibility of human oversight and adaptability for complex tasks. This collaborative approach combines human judgment with robotic precision, enhancing both efficiency and workplace morale.
Challenges and Limitations of Automation in Manufacturing
While automation offers numerous advantages, it also presents challenges. Some of the primary challenges include:
a) High Initial Investment
Implementing automation requires a significant upfront investment in equipment, software, and workforce training. Small and medium-sized manufacturers may find these costs prohibitive.
b) Workforce Displacement
The shift toward automation has led to concerns about job displacement. As machines take over repetitive tasks, the demand for manual labor declines, potentially leading to job losses. However, it also creates opportunities for workers to upskill and take on new roles related to automation oversight and maintenance.
c) Cybersecurity Risks
Automated systems are vulnerable to cyber-attacks, as they rely on digital infrastructure. A breach can disrupt operations, damage equipment, and lead to significant financial losses. Therefore, manufacturers need to invest in cybersecurity to protect their automated systems.
d) Maintenance and Downtime
Automated systems require regular maintenance to function correctly. Unplanned downtime due to equipment malfunction can disrupt production schedules and result in financial losses. Companies must have robust maintenance protocols to minimize such risks.
Addressing these challenges requires strategic planning, investment in workforce training, and a commitment to cybersecurity.
The Future of Automation in Manufacturing
As technology advances, automation’s role in manufacturing will continue to expand. Emerging trends in the field include:
a) Artificial Intelligence and Machine Learning
AI and machine learning can analyze massive amounts of data, helping manufacturers predict equipment malfunctions, optimize supply chains, and customize production. AI is becoming increasingly crucial for predictive maintenance, enhancing uptime and reducing unexpected breakdowns.
b) Internet of Things (IoT)
The IoT connects machinery and devices across the manufacturing floor, enabling real-time data collection and analysis. Through IoT, companies can monitor production in real-time, track equipment health, and optimize operations remotely, driving efficiency and reducing downtime.
c) Additive Manufacturing and 3D Printing
3D printing allows companies to produce custom components quickly and cost-effectively. In the future, manufacturers may increasingly use 3D printing alongside traditional methods for rapid prototyping and on-demand production, enabling more flexible manufacturing solutions.
d) Sustainable and Eco-Friendly Automation
As sustainability becomes more critical, automation technologies will focus on energy efficiency and waste reduction. From green manufacturing practices to eco-friendly production methods, automation will help manufacturers reduce their environmental impact.
These innovations highlight automation’s transformative potential and underscore its role in future-proofing the manufacturing industry.
Conclusion
Automation in the manufacturing industry has redefined how companies operate, offering numerous advantages such as enhanced productivity, consistent quality, and cost savings. However, it also presents challenges, from high initial costs to workforce displacement. To remain competitive, manufacturers must embrace automation thoughtfully, addressing these challenges while exploring new technologies like AI, IoT, and 3D printing.
In a rapidly evolving industry, automation is no longer optional—it is essential for manufacturers looking to thrive in a globalized economy. By investing in automation, companies can enhance efficiency, drive innovation, and secure a competitive edge in the marketplace.