Advancements in technology and supply chain practices are revolutionizing the metal fabrication industry, transforming it from a straightforward process of cutting, welding, machining, and assembly into a dynamic and complex landscape. As the industry evolves, its growth increasingly hinges on key sectors such as aerospace, automotive, energy, and construction. This shift compels metal shops to enhance profitability through customer diversification and precise demand forecasting. In this context, staying informed about the latest metal fabrication trends is essential for businesses aiming to navigate the challenges and seize the opportunities presented by this rapidly changing environment. Here are some of the most significant trends gaining traction in the metal fabrication industry.
Overview of the Metal Fabrication Industry
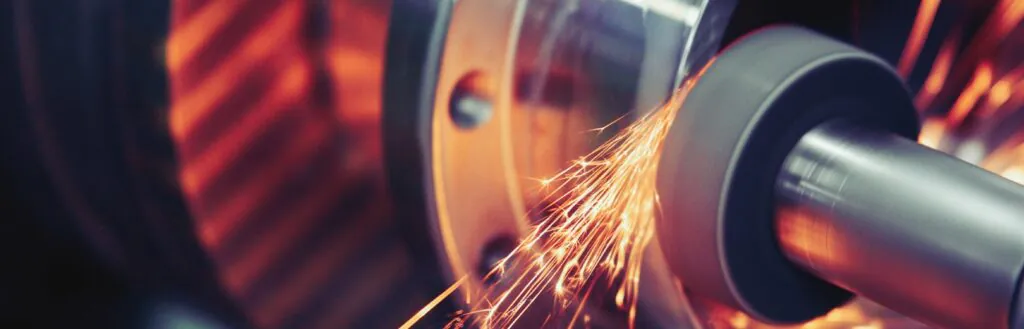
The metal fabrication industry involves the transformation of raw metal materials into finished products through various processes such as cutting, shaping, bending, welding, and assembly. This sector serves a diverse range of applications across industries including automotive, aerospace, construction, and electronics, making it a vital component of the global economy.
Factors Driving Metal Fabrication Industry Growth
The metal fabrication industry is experiencing robust growth driven by several key factors. Here are the primary elements propelling this expansion:
-
Increasing Demand for Manufactured Goods:
The global appetite for manufactured products is on the rise, particularly in emerging economies like China and India. This demand is fueled by population growth, a burgeoning middle class, and heightened consumer needs.
-
Technological Advancements:
Innovations such as automation, robotics, and 3D printing are revolutionizing metal fabrication. These technologies enhance efficiency, precision, and customization, allowing manufacturers to meet diverse market demands effectively.
-
Sustainability Pressures:
There is a growing emphasis on environmental sustainability, pushing metal fabricators to adopt eco-friendly practices. This includes minimizing waste and energy consumption, as well as utilizing recyclable materials to align with regulatory standards and consumer preferences.
-
Aerospace and Automotive Industry Needs:
The aerospace and automotive sectors are increasingly seeking lightweight materials to improve energy efficiency and performance. This trend is driving demand for advanced alloys and innovative fabrication techniques.
-
Infrastructure Investments:
Significant investments in infrastructure development, particularly in renewable energy and construction, are creating a robust demand for fabricated metal components. Government initiatives aimed at modernizing infrastructure further bolster this growth.
-
Customization and Innovation:
The need for unique, tailored products is prompting metal fabricators to innovate continuously. Companies that can provide customized solutions gain a competitive edge in the market.
-
Globalization and Market Expansion:
The globalization of trade has opened new markets, enabling metal fabricators to expand their reach and capitalize on international collaborations, particularly in emerging economies.
-
Skilled Labor Shortages:
While the industry faces challenges related to a shortage of skilled labor, companies are responding by investing in training programs and adopting technologies that enhance workforce productivity.
These factors collectively contribute to a positive outlook for the metal fabrication industry, positioning it for sustained growth and innovation in the coming years.
Top 8 Game-Changing Trends and Technologies Shaping Metal Fabrication Industry
The metal fabrication industry is undergoing a transformative phase, driven by the adoption of cutting-edge technologies and innovative practices. As we move forward into 2024, these emerging trends and advancements are poised to revolutionize the way metal fabrication is approached, offering increased efficiency, cost savings, and competitive advantages. Let’s explore top 8 game-changing metal fabrication trends that will shape the future of this dynamic industry.
Automation and Collaborative Robotics:
Automation is transforming metal fabrication by streamlining cutting and bending processes, enabling machines to operate without human oversight, and significantly reducing labor costs.
3-D Printing and Additive Manufacturing:
The rise of 3D printing in metal fabrication allows for the creation of complex tools and structures, enhancing design flexibility and reducing material waste compared to traditional methods.
Nearshoring:
As manufacturers respond to rising logistics costs and market volatility, nearshoring is becoming a strategic choice, bringing production closer to home to capitalize on local tax incentives.
Adoption of ERP Systems:
Metal fabrication companies are increasingly implementing ERP systems to manage operations and supply chains more effectively, enhancing productivity and streamlining critical business functions.
Sustainable Practices:
The push for sustainability in metal manufacturing is driving the adoption of eco-friendly materials, recycling initiatives, and alternative energy sources to minimize environmental impact.
Digital Twins and Simulation:
Digital twin technology allows manufacturers to create virtual models of their operations, optimizing processes and predicting maintenance needs to enhance overall efficiency.
Internet of Things (IoT) and Industry 4.0:
IoT integration in metal fabrication provides real-time data monitoring and predictive maintenance capabilities, improving operational efficiency and reducing equipment downtime.
Computer-Aided Design (CAD) and Computer-Aided Manufacturing (CAM):
The use of CAD and CAM software enhances precision in metal fabrication, allowing for detailed modeling and efficient programming of CNC machines to improve product accuracy and reduce lead times.
Automation and Collaborative Robotics
Automation has drastically changed the outlook of many industries, and the metal fabrication industry is no exception. Automation has helped metal shops simplify the act of cutting and bending sheet metal; thereby, shortening the overall operations and improving the order-to-ship cycles. Additionally, automation has allowed manufacturers to cut metals without human supervision for days at a stretch and consequently save metal fabricators a large part of human resources cost. Moreover, the integration of advanced robotics and IoT technologies further enhances operational efficiency by enabling real-time data collection and predictive maintenance.
3-D Printing and Additive Manufacturing
3D printing is a relatively new technology and has been used in the manufacturing industry to make product prototypes. However, things are looking quite exciting for the metal industry as more and more metal fabrication businesses are planning to invest in this technology to create simple and sophisticated tools and structures. Metal 3D printing differs from traditional steel fabrication processes as it involves the stamping of metals to produce a required design. For instance, SpaceX relied on 3D printing of custom metal parts for the combustion chamber of the SpaceX SuperDraco engine.
Nearshoring
Outsourcing has been the go-to-market strategy for any manufacturing industry. The availability of low-cost manufacturing locations such as China and India was seen as a lucrative option for manufacturers. However, that view is rapidly changing as metal fabricators need to respond to dynamic home demands, factor in rising logistics costs, drive innovation, and prepare against market volatility risks. More and more manufacturers are reshoring their manufacturing capacities back to the American market as the tangible benefits outweigh the labor cost difference. Nearshoring operations have also been helped by local tax incentives and the “Made in America” movement.
Adoption of ERP Systems
The majority of the metal fabrication companies operate across a wide geography, both local and global markets. Since they also carry out custom metal fabrication, it can be quite challenging to manage all their operations and their suppliers, sourcing materials, and other processes across the supply chain. As a result, metal fabrication companies are resorting to ERP software to streamline their operations and increase their productivity. ERP software goes well beyond excel sheets and software like Tally to reliably manage all critical business functions such as operational performance planning, enterprise mobilization, demand forecasting, and resource planning.
Sustainable Practices
The future of metal manufacturing is intrinsically tied to sustainability. Environmental concerns and regulations are driving the industry towards greener practices. This includes using more eco-friendly materials, reducing energy consumption, and minimizing waste. One notable development is the increased use of recycled metals in fabrication processes. Recycling not only conserves natural resources but also reduces the carbon footprint of metal fabrication. Furthermore, manufacturers are exploring alternative energy sources, such as solar and wind power, to power their operations, reducing their reliance on fossil fuels.
Digital Twins and Simulation
Digital twin technology is gaining momentum in metal fabrication. A digital twin is a virtual representation of a physical object or system, allowing for real-time monitoring and analysis of production processes. By creating a digital twin of a metal fabrication facility, manufacturers can optimize operations, predict maintenance needs, and improve overall efficiency. Simulation software is also playing a crucial role, enabling manufacturers to test various scenarios and optimize production workflows before actual fabrication begins. This reduces material waste and enhances resource utilization, contributing to more efficient manufacturing practices.
Internet of things (IoT) and Industry 4.0
The Internet of Things (IoT) is increasingly vital in controlling metal fabrication equipment. By integrating IoT devices and sensors into machinery, companies can access real-time data on performance and usage. This analysis optimizes operations and maintenance, leading to enhanced efficiency and cost savings. Additionally, IoT-enabled machinery allows for remote monitoring and control, fostering flexibility and collaboration among teams and facilities. This technology also supports predictive maintenance, using data from machines and sensors to forecast maintenance needs, reducing downtime and extending equipment lifespan.
Computer-Aided Design (CAD) and Computer-Aided Manufacturing (CAM)
The integration of Computer-Aided Design (CAD) and Computer-Aided Manufacturing (CAM) software is increasingly prevalent in metal fabrication, enhancing precision and efficiency in the design and manufacturing processes. CAD software allows designers and engineers to create detailed 3D models of parts or products, which can be simulated and tested before actual fabrication begins, minimizing errors and material waste.
CAM software, in turn, efficiently programs CNC machines to execute fabrication processes according to the specifications of the CAD models. This integration leads to improved accuracy and consistency in the final products, as well as reduced lead times and costs. Additionally, CAD and CAM systems can be integrated with other digital technologies, such as IoT and simulation software, to further enhance the overall efficiency and automation of the fabrication process.
Real-World Examples
Company Name | Country | Current Metal Fabrication Trends Utilized |
---|---|---|
O’Neal Manufacturing Services | U.S. | Automation and robotics for enhanced efficiency and precision in production. |
Interplex Holdings Pte. Ltd. | Singapore | Adoption of sustainable practices and eco-friendly materials. |
Komaspec | China | Implementation of 3D printing and additive manufacturing for customization. |
BTD Manufacturing | U.S. | Use of CNC machining for precision fabrication and rapid prototyping. |
TRUMPF | Germany | Integration of digital twin technology for real-time monitoring and optimization. |
Mazak Corporation | Japan | Advanced automation solutions to streamline manufacturing processes. |
C&C Fabrications | U.K. | Customization and bespoke fabrication solutions using advanced design software. |
DMG MORI | Germany | Focus on Industry 4.0 technologies, including IoT integration for smart manufacturing. |
Conclusion
The metal fabrication industry is poised for significant growth and transformation as it embraces innovative technologies and practices. As we move into 2024, the trends discussed highlight the industry’s commitment to enhancing efficiency, sustainability, and adaptability in response to evolving market demands. Automation, 3D printing, IoT integration, and advanced materials are not just shaping the future of metal fabrication; they are redefining it.
By leveraging these advancements, metal fabricators can improve operational performance, reduce costs, and create more customized solutions for their clients. As the industry continues to navigate challenges such as labor shortages and supply chain disruptions, staying informed about these trends will be crucial for businesses looking to maintain a competitive edge. Embracing these changes will not only foster innovation but also contribute to a more sustainable and efficient future for the metal fabrication sector.
Related Articles
- How We Drove 29% Profit Growth and Record Sales for a Pharmaceutical Company Through Pharma Market Intelligence
- How We Helped a Leading Online Game Developer Navigate and Capitalize on the Growing Virtual Goods Market
- Market Segmentation Helps a Leading Transportation and Logistics Industry Client Refine Their Marketing Strategies